Epoxy Resin Modification
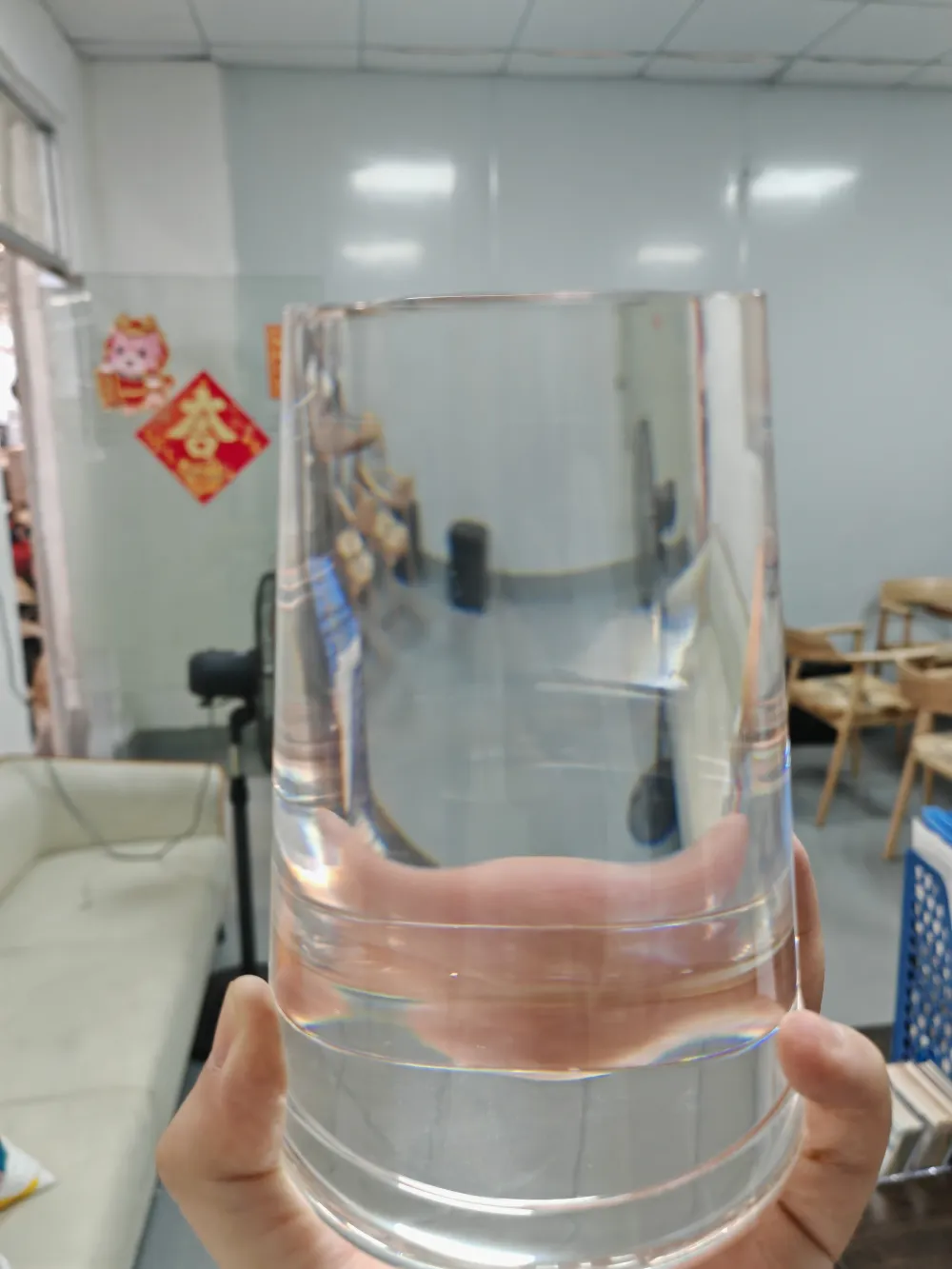
The toughness of epoxy resin depends primarily on its molecular structure, with crystal structures providing toughness as a component of toughness. Changes to this structure may alter intermolecular bonding patterns thereby impacting toughness of resin resin. Epoxy resins generally display excellent mechanical properties; however, under specific conditions (surface tension or pH fluctuations), they can fail. Epoxy resins offer superior electrical insulation, heat resistance, chemical corrosion resistance, mechanical aging resistance and organic solvent compatibility; making them an indispensable material. Modified epoxy resins acquire additional functionalities which further increase performance. As epoxy resin applications expand, materials engineers need to conduct modification studies more frequently in order to enhance heat and corrosion resistance while still meeting mechanical properties requirements. To maintain mechanical properties while increasing heat and corrosion resistance.
1. Analysis of Major Content Modifiers of Epoxy Resin
1.1 Toughening With Rubber Elastomers
Incorporating rubber elastomers into epoxy resin results in their active end groups reacting perfectly with functional groups in the epoxy system, further heightening its toughening effects. As soon as researchers realized CTBN rubber’s significant role in improving resin toughness, studies on various rubber types intensified, significantly improving modification outcomes – commonly chloroprene, nitrile, and butyl acrylate rubbers became widely utilized; their incorporation alters solubility parameters, controls gelation processes while employing rubber particles that prevent cracking reinforce surface toughness to enhance surface toughness further.
Research systems for rubber-modified epoxy resins both domestically and internationally typically fall into one of two categories: using CTBN rubber, or mixing liquid rubbers such as silicone or polybutadiene into liquid rubber mixtures such as the latter two cases. Careful planning exists for designing methods of manufacturing process control as well as controlling reactions processes. Before conducting toughening experiments, rubber-modified materials must first be prepared, tested for modification capabilities using infrared spectroscopy analysis and subjected to modification tests. Modifying silicone rubber and testing its impact resistance with epoxy resin has demonstrated its impact-increasing effects; for instance, adding modified silicone rubber significantly increased toughness if its impact resistance decreased considerably after modification. Reactive liquid rubbers and polysulfide rubbers were also utilized during these studies for modification purposes – incorperating metal oxides or organic amine curing agents can create two-component coatings with versatile properties.
1.2 Toughening through Resin Alloying Resin-alloyed epoxy resins offer superior toughness compared to rubber-toughened ones, thanks to resin alloying’s ability to overcome rubber’s inherent restrictions for heat resistance and rigidity improvements, and thermoplastic resins chemically reacting with epoxy surfaces chemically creating high molecular weight alloyed materials with enhanced toughness such as polyimide, polyphenylene oxide or liquid crystalline polymers as examples of thermoplastic thermoplastic resins achieving high toughness levels; these include polyimide, Polyimide Polyphenylene oxide as well as liquid crystalline polymers among many others.
Domestic researchers have utilized in-situ polymerization to optimize the internal structure of epoxy resins by altering polyurethane molecular structures. When the cured resin contains low polyurethane concentration, rigid molecules distribute evenly in its matrix to form composite high molecular weight materials with increased tensile strength that serve as reinforcement.
Studies conducted using PSF resin (polysulfone) examined molecular weight effects on epoxy resin toughness. Experimental findings indicate that increasing PSF molecular weight significantly improves toughness; increasing it to around 20% can increase toughness by four. Polyetherimide (PEI) can also be added to increase fracture toughness; using 25% PEI will elevate fracture toughness up to 2000 MPa with increasing pressure; simultaneously improving both flexural strength and surface toughness as pressure rises. Microscopic examination reveals dual-continuous structures within modified resins which indicate increased surface toughness.
1.3 Toughening via Flexible Segment Curing Agents
Flexible segment curing agents can improve crosslinked networks found within epoxy resins to produce tighter structures after curing has taken place, as seen through microphase separation occurring after cure time and dense network formation after curing has finished. This approach is both simple and effective – perfect for broad applications!
Organic compounds with flexible chains chemically react with epoxy groups to form new resins with improved strength and adhesion properties. Acrylate-modified epoxy resins produce epoxy acrylate coatings with superior bonding stability; international studies often employ terminal amino polyether ketone curing agents composed of various combinations such as polybisphenol A ether ketone or polyisobutylene ether ketone to provide high molecular weight curing agents that increase chain flexibility at crosslinking points for increased strength while still maintaining surface characteristics of epoxy resin surfaces
2.Toughening Measures for Epoxy Resin
2.1 Select and Manage Modifiers It is crucial that appropriate modifiers be selected due to the wide array of adhesive types and properties; polyamide adhesives may often be chosen but could compromise material properties; key considerations here could include:
1.Compatibility between epoxy resin and solid components.
2. Thermal stability below 200degC.
3. Maintaining strong compatibility between solid epoxy components.
To achieve successful toughening, control curing time and optimize modifier quantities. Optimizing ratios improve compatibility, adhesion, and mechanical performance – such as increasing SiO2 content so as to enhance compatibility between SiO2 phases and epoxy polymers.
2.2 Mechanical Processing Modifications Mechanical processing modifications involve shaping epoxy resin into components and applying adhesives or coatings that provide wear resistance. Chemical processes can alter mechanical properties while tougheners (polymers and metallic adhesives) improve strength and durability; though effective, such modifications must take into consideration both longevity and operational durability to be truly successful.
Light initiators enhance post-cure strength and toughness by activating oxidation reactions in polymers cured through UV curing processes, thus decreasing defects that form after curing has taken place. Common initiators such as zinc oxide or methyl benzoate should be tailored specifically to curing conditions for maximum performance.
Coating toughening uses polymers or curing agents to form dense protective films on substrates that offer corrosion resistance, UV protection, insulation benefits and insulation properties. Water-based coatings – widely applied by aerospace industries such as Boeing – offer environmental advantages while improving adhesion.
To increase the stability and strength of the structure, its foundational components need to be in good shape.
3、Conclusion
This research investigates epoxy resin toughening modifications and strategies. As industry demands evolve, epoxy resin applications require modifications that enhance functionality and value; research into modifiers and techniques is crucial in improving epoxy resin performance for continued industrial progress.